3D打印技術(shù)又被稱為“快速成形技術(shù)”、“增材制造技術(shù)”和“實(shí)體自由制造”等,其思想最早在19 世紀(jì)末出現(xiàn)于美國(guó),并在20 世紀(jì)80 年代得到應(yīng)用與發(fā)展,至今已有30 多年[1-2]。3D打印技術(shù)基于離散-堆積原理,采用與減材制造技術(shù)相反的加工方式(逐層累加),通過操作計(jì)算機(jī)使材料逐層累加,最終得到立體實(shí)物的過程[3-7]。相比于傳統(tǒng)的
減材制造技術(shù),3D打印技術(shù)具有精度高、工藝簡(jiǎn)單、自由度高、節(jié)約原材料、節(jié)省時(shí)間等優(yōu)點(diǎn),在航空航天、工業(yè)、國(guó)防、醫(yī)療、汽車、電子等領(lǐng)域得到了廣泛的應(yīng)用[8-9]。目前可用于3D打印的原料主要有高分子材料(樹脂、塑料、橡膠等)、金屬材料(鋁合金、鈦合金、不銹鋼等)和非金屬材料(陶瓷、石膏、紙張等),其中高分子材料和非金屬材料3D打印技術(shù)起步較早、研究較多,技術(shù)相對(duì)成熟[8]。而金屬材料3D打印技術(shù)則具備巨大的發(fā)展?jié)摿Γ袑<翌A(yù)測(cè),在未來制造業(yè)中,金屬材料3D打印技術(shù)將會(huì)逐漸占據(jù)整個(gè)快速成形制造領(lǐng)域的主導(dǎo)地位[10]。
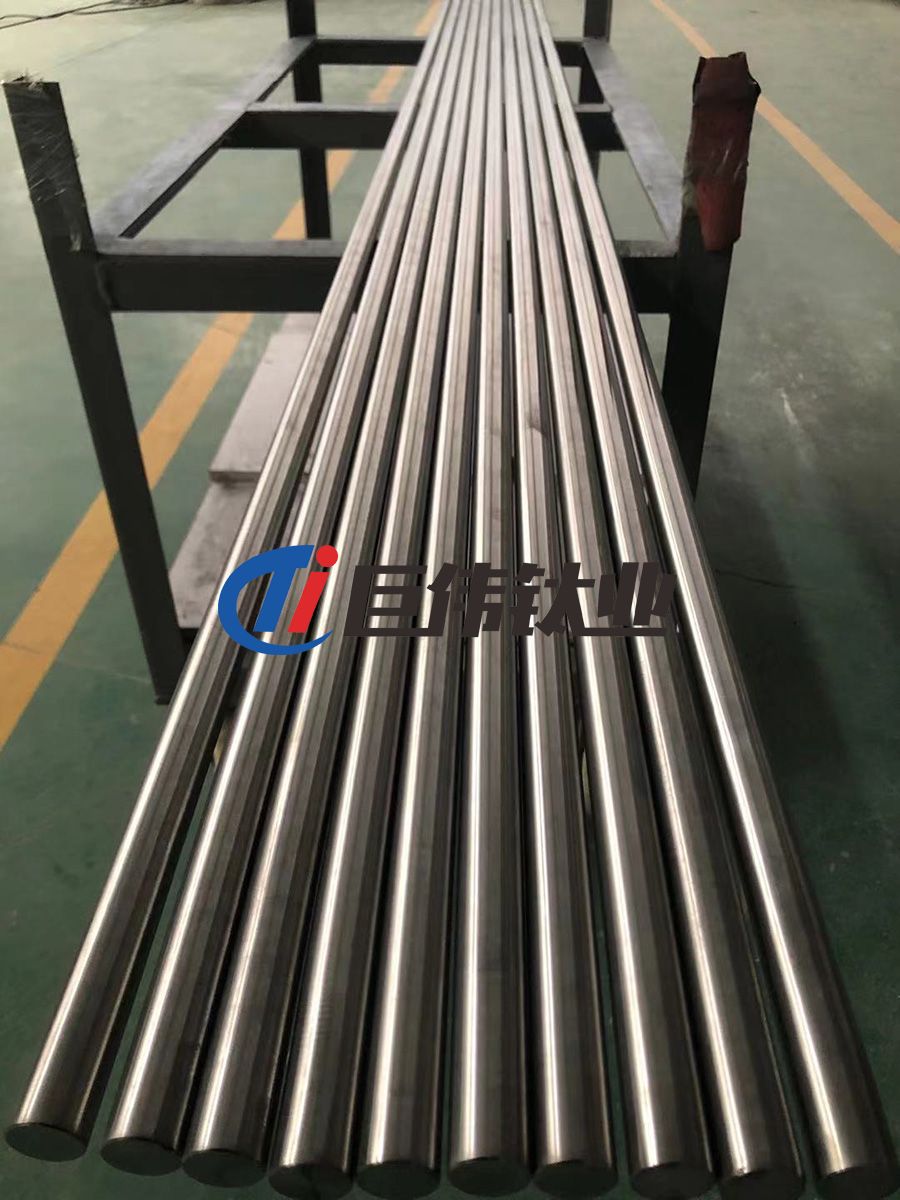
鈦合金是一種重要的有色金屬,具有密度小、比強(qiáng)度高,以及良好的耐腐蝕性能、高溫變形性能和生物相容性等諸多優(yōu)點(diǎn),在航空航天、工業(yè)、國(guó)防、醫(yī)療等領(lǐng)域得到廣泛應(yīng)用[1, 11-12]。傳統(tǒng)的鍛造和鑄造方法所制得的大型復(fù)雜的鈦合金構(gòu)件,由于成本高、工藝復(fù)雜、材料利用率低以及后續(xù)加工困難等不利影響,嚴(yán)重阻礙了其更為廣泛的應(yīng)用。而3D打印技術(shù)采用與傳統(tǒng)的減材制造相反的加工方法,有著極高的材料利用率,相比傳統(tǒng)的成形加工方法有著極大的優(yōu)勢(shì)。目前對(duì)鈦合金3D打印的研究主要集中在材料、設(shè)備、技術(shù)以及工藝方面,但是對(duì)零件的成形過程中缺陷問題的研究還處于初步階段。本文綜述了國(guó)內(nèi)外幾種常用的鈦合金3D打印技術(shù),重點(diǎn)介紹了其在成形過程中缺陷的分類、危害以及形成原因的研究現(xiàn)狀,并結(jié)合國(guó)內(nèi)外的研究進(jìn)展,對(duì)合金缺陷的改善方法進(jìn)行探討,對(duì)鈦合金3D打印的發(fā)展前景進(jìn)行展望。
1、鈦合金3D打印技術(shù)分類
當(dāng)今,國(guó)內(nèi)外常用的鈦合金3D打印方法主要有以下幾種。根據(jù)熱源不同可分為:以激光為熱源的激光選區(qū)燒結(jié)成形技術(shù)(selective laser sintering,SLS)、激光選區(qū)熔化成形技術(shù)(selective laser melting,SLM)和激光近凈成形技術(shù)(laser solid forming,LSF);以電子束為熱源的電子束選區(qū)熔化成形技術(shù)(electron beam selective melting, EBSM)和電子束熔絲沉積成形技術(shù)(electron beam fuse depositionforming, EBF3)。
SLS 技術(shù)基于激光粉末床,運(yùn)用激光有選擇地對(duì)粉末進(jìn)行燒結(jié),逐層疊加得到最終的實(shí)體零件。
具有材料利用率高、適用范圍廣、無(wú)需模具和支撐結(jié)構(gòu)、可直接制造任意形狀復(fù)雜的結(jié)構(gòu)件等優(yōu)點(diǎn);但是由于燒結(jié)過程中粉末沒有完全熔化,且之間沒有受到壓力,因此孔隙無(wú)法消除,最終得到的制件性能與傳統(tǒng)制件相比仍有較大差距,存在殘余應(yīng)力大、致密度低、強(qiáng)度低等缺陷[10]。
LSF 技術(shù)采用同步送粉方式,在激光作用下鈦合金粉末開始熔化、凝固,逐層堆積,可實(shí)現(xiàn)鈦合金零件直接制造。該技術(shù)具有低成本、周期短、無(wú)需模具、材料利用率高等優(yōu)點(diǎn),但成形精度低,屬于“近凈成形”,需經(jīng)過后續(xù)加工才能得到最終的制件[9]。
在SLS 技術(shù)基礎(chǔ)上發(fā)展起來的SLM 技術(shù)所使用的激光功率更大,整個(gè)加工進(jìn)程都處于保護(hù)氛圍的成形艙內(nèi), 金屬粉末完全熔化, 成功彌補(bǔ)了SLS 技術(shù)只能成形低熔點(diǎn)金屬、孔隙大、力學(xué)性能差等缺點(diǎn)[13-14];成形件的精度高和表面質(zhì)量好,無(wú)需后續(xù)加工,屬于“凈成形”,但是可成形的尺寸有限,且成本較高。
EBSM 技術(shù)與SLM 技術(shù)的成形原理基本相似,主要區(qū)別在于EBSM 技術(shù)采用能量更大的電子束為熱源,整個(gè)成形過程均在真空環(huán)境中(≤10–2Pa)進(jìn)行,能夠很好地防止空氣中其他有害雜質(zhì)C、N、O 等的影響。具有成形速率快、能量密度高、無(wú)反射、聚焦方便、真空無(wú)污染、尺寸精度高、力學(xué)性能好等優(yōu)點(diǎn)[15-17]。
基于LSF 技術(shù)基礎(chǔ)發(fā)展起來的EBF3 技術(shù),具有成形效率快、無(wú)反射、材料和能量的利用率高、真空無(wú)污染等優(yōu)點(diǎn),適合大中型鈦合金零件的成形制造修復(fù)。以絲材代替粉末為原料雖然避免了吹粉問題,但是其成形精度差,需要后續(xù)表面處理[18-19]。
表1 為幾種常見的鈦合金3D打印技術(shù)比較。
綜合對(duì)比,EBSM 技術(shù)是未來最具發(fā)展前景的鈦合金3D打印技術(shù),理由如下:(1) EBSM 具有與SLM 技術(shù)相當(dāng)?shù)某尚尉取⒈砻尜|(zhì)量以及良好的力學(xué)性能,而且也克服了SLM 技術(shù)不能成形大尺寸零件的缺點(diǎn);(2)整個(gè)成形過程均在真空環(huán)境下進(jìn)行,有效防止成形過程中C、N、O 元素對(duì)材料的污染;(3)采用功率更大的電子束代替激光束,不但
加快成形效率,而且降低生產(chǎn)成本。
2、3D打印成形鈦合金構(gòu)件缺陷分析
采用3D打印技術(shù)制備鈦合金,成功克服了使用傳統(tǒng)方法制備鈦合金結(jié)構(gòu)件時(shí),所面臨的費(fèi)用高、材料浪費(fèi)嚴(yán)重、加工工藝復(fù)雜,以及后續(xù)加工困難等不利因素,但采用3D打印技術(shù)成形鈦合金零件時(shí),由于粉末/絲材特殊的加工性能,或者工藝參數(shù)選擇不當(dāng),工件容易出現(xiàn)球化、裂紋、孔隙以及翹曲變形等缺陷。如圖1 所示,嚴(yán)重影響鈦合金的機(jī)械性能和成形精度,阻礙了鈦合金3D打印技術(shù)的發(fā)展。另外,缺陷無(wú)損檢測(cè)是3D打印件能否實(shí)現(xiàn)廣泛應(yīng)用的基礎(chǔ),也是影響3D打印技術(shù)進(jìn)一步發(fā)展的決定因素。目前,國(guó)內(nèi)外對(duì)3D打印件缺陷進(jìn)行無(wú)損檢測(cè)的方法主要有[ 2 0 - 2 2 ]:滲透檢測(cè)、X 射線檢測(cè)、磁粉檢測(cè)和超聲檢測(cè)等。隨著3D打印件向結(jié)構(gòu)大型化、復(fù)雜化和精細(xì)化方向發(fā)展,傳統(tǒng)的無(wú)損檢測(cè)方法已經(jīng)不再適用于3D打印件的缺陷檢測(cè)和分析,新型的無(wú)損檢測(cè)技術(shù)工業(yè)CT 檢測(cè)和激光超聲在線無(wú)損檢測(cè)相繼問世。Plessis 等[23]采用CT 技術(shù)檢測(cè)3D打印成形的復(fù)雜鈦合金結(jié)構(gòu)件,成功檢出了孔隙率僅為0.005% 的微孔隙,這在采用常規(guī)無(wú)損檢測(cè)方法是幾乎不可能檢出的。國(guó)內(nèi)一專利[24]發(fā)明了激光超聲無(wú)損檢測(cè)技術(shù),利用激光激勵(lì)的超聲表面波幅的變化檢測(cè)3D打印過程中產(chǎn)生的缺陷,實(shí)現(xiàn)制造過程同步對(duì)零件進(jìn)行檢測(cè)。
表2 列出幾種常見的無(wú)損檢測(cè)技術(shù)比較。
隨著科學(xué)技術(shù)的進(jìn)步,3D打印技術(shù)也在不停地完善和發(fā)展,目前國(guó)內(nèi)外逐漸對(duì)這些缺陷形成的原因、分類及其危害進(jìn)行了大量的研究,以期使鈦合金3D打印技術(shù)得到更為廣泛的應(yīng)用。
2.1 球化現(xiàn)象
球化現(xiàn)象是3D打印金屬材料成形過程中常見的一種缺陷,是指金屬粉末經(jīng)激光或電子束熔化后,不能均勻地鋪展于前一層,而是產(chǎn)生大量相互隔離的球狀金屬,這種現(xiàn)象被稱為球化現(xiàn)象[25]。該缺陷主要的危害有以下兩個(gè)方面:(1)導(dǎo)致金屬件組織內(nèi)部存在孔隙,大大降低成形件的力學(xué)性能并增加了表面粗糙度;(2)凝固后的金屬球又會(huì)使下一層的鋪粉不均勻,且鋪粉輥又會(huì)與前一層所產(chǎn)生的金屬球相互摩擦,不但會(huì)破壞成形件的表面質(zhì)量,而且當(dāng)他們之間摩擦非常大時(shí),鋪粉輥將無(wú)法動(dòng)彈,致使成形過程終止。
近年來,越來越多的學(xué)者對(duì)球化現(xiàn)象形成原因進(jìn)行了大量的研究,但各持不同的意見。其中“液態(tài)金屬與固態(tài)表面的潤(rùn)濕問題”的說法較為普遍接受[26]。球化根據(jù)尺寸不同可分為大尺寸球化和小尺寸球化,對(duì)大尺寸球化的形成原因歸結(jié)于液-固潤(rùn)濕問題。圖2 所示為液態(tài)金屬與固態(tài)金屬的潤(rùn)濕示意圖,當(dāng)熔融金屬液均勻鋪展時(shí),潤(rùn)濕角θ <90°,固液金屬潤(rùn)濕性良好,不會(huì)出現(xiàn)球化,當(dāng)金屬液很難鋪展于固態(tài)表面時(shí),θ > 90°,固液金屬潤(rùn)濕性差,產(chǎn)生球化反應(yīng)。對(duì)于小尺寸球化的成因,則認(rèn)為是加工過程中發(fā)生液滴飛濺,在熔道或熔道周圍凝固成金屬球,因?yàn)榻饘僖猴w濺相對(duì)較少,所以金屬球的尺寸也較小。Sallica 等[12]通過研究SLM成形件Ti-6Al-4V 的微觀組織,發(fā)現(xiàn)過高的激光功率會(huì)減小熔融金屬的表面能,并導(dǎo)致球化現(xiàn)象的產(chǎn)生。張曉博[27]研究了加工環(huán)境對(duì)球化現(xiàn)象的影響,認(rèn)為成形氣氛中的氧元素容易與熔融金屬液發(fā)生反應(yīng),形成一層致密的氧化物薄膜,該薄膜并不利于金屬液與固體基底潤(rùn)濕、粘合,容易導(dǎo)致球化的產(chǎn)生,且球化現(xiàn)象隨氧含量的增加,效果越明顯;他還研究了工藝參數(shù)對(duì)球化現(xiàn)象的影響,認(rèn)為激光功率過高,會(huì)出現(xiàn)“飛濺”,導(dǎo)致熔道間的金屬球大量出現(xiàn),球化現(xiàn)象明顯;掃描速率過快,激光在粉末上停留的時(shí)間較短,金屬液溫度低,流動(dòng)性及潤(rùn)濕性差導(dǎo)致球化現(xiàn)象明顯。沈以赴等[15]認(rèn)為球化是由于液相表面張力大、黏度高,或熔融粉末與未熔化的粉末顆粒和基板未發(fā)生浸潤(rùn)等的影響下產(chǎn)生,進(jìn)一步分析表明,激光快速成形過程中的氧氣是導(dǎo)致球化的直接原因。Gusarov 等[28]借助Plateau-Rayleigh 毛細(xì)不穩(wěn)定理論[29]指出:球化現(xiàn)象與熔池的幾何形狀密切相關(guān),在二維層面上,熔池長(zhǎng)度與寬度的比值大于2.1 時(shí),容易出現(xiàn)球化現(xiàn)象。
2.2 孔隙
孔隙是成形過程中的另一種重要缺陷,對(duì)于一些高性能致密的鈦合金制件,由于孔隙的存在嚴(yán)重降低了制件的力學(xué)性能和致密性,阻礙了鈦合金的廣泛應(yīng)用。對(duì)于孔隙的成因研究報(bào)道較多,上面談到的球化現(xiàn)象會(huì)引起制件的孔隙問題;裂紋也會(huì)導(dǎo)致孔隙的形成,隨著裂紋尺寸的不斷變大,裂紋會(huì)相遇連接,最后形成孔隙;另外粉末本身的缺陷也會(huì)導(dǎo)致孔隙產(chǎn)生,在快速熔化和凝固過程中,空心粉中含有的氣體來不及逃逸,從而在成形件中殘留形成孔隙,此類孔隙形貌多為球形或類球形。
Gong 等[30]通過使用較大范圍的工藝參數(shù)成形Ti-6Al-4V 合金,根據(jù)孔隙率大小將工藝參數(shù)進(jìn)行分類,并對(duì)孔隙的產(chǎn)生機(jī)理進(jìn)行了討論。薛雷等[31]分別采用未經(jīng)干燥處理和經(jīng)真空干燥處理的TC4粉末對(duì)制件進(jìn)行激光快速修復(fù),認(rèn)為修復(fù)過程中孔隙的形成原因歸因于以下兩種:(1)粉末鋪放時(shí)吸附了空氣中的其他雜質(zhì)氣體,在隨后的成形過程中受到激光/電子束加熱、熔化后,又經(jīng)快速凝固得到成形件,其組織內(nèi)部的氣體析出不及時(shí),保留在成形件中并形成孔隙;(2)粉末不夠干燥且存在水分,在加熱熔融后,一部分在熔池表面附近的水分以水蒸氣的形式蒸發(fā)逸出;遠(yuǎn)離熔池表面的另一部分水分,與(1)類似的情況,由于氣體來不及逸出,在制件內(nèi)部產(chǎn)生氣孔。Zaeh 等[32]研究發(fā)現(xiàn),使用高能量密度的熱源加工時(shí),容易造成受熱不均,當(dāng)某部分熱量過高時(shí),即使粉末還未引起球化現(xiàn)象,但仍會(huì)形成孔洞,并且空洞在后續(xù)的加工過程中會(huì)變長(zhǎng)。
Sallica 等[12]研究發(fā)現(xiàn)當(dāng)激光功率過低時(shí),導(dǎo)致熔化不完全從而引起孔隙,影響致密性。
2.3 裂紋
裂紋是激光快速成形過程中影響極大的一種缺陷。在成形過程中,由于熔體過冷度大、冷卻速率快,在冷卻過程中應(yīng)力得不到釋放而保留在制件內(nèi),當(dāng)應(yīng)力集中超過材料屈服強(qiáng)度就會(huì)產(chǎn)生裂紋[27]。裂紋通常可分為微觀裂紋和宏觀裂紋兩種,其中成形件組織內(nèi)部的微觀裂紋一般是凝固裂紋,歸類為熱裂紋;宏觀裂紋則大部分表現(xiàn)為層間裂紋,屬于冷裂紋范疇。若制件中存在裂紋,將嚴(yán)重影響制件的組織和力學(xué)性能。微裂紋尺寸相對(duì)較小,會(huì)降低抗疲勞性能,縮短成形件的使用壽命;對(duì)于粗裂紋而言,會(huì)影響零件的使用性能,甚至導(dǎo)致零件直接報(bào)廢。
周旭等[33]研究了近α 鈦合金激光選區(qū)熔化成形的開裂機(jī)理,得出如下結(jié)論:在殘余應(yīng)力作用下,裂紋形成于側(cè)壁缺口,在沉積層上沿著硬脆化合物擴(kuò)大。張升等[34]采用交替掃描策略制備出TC4 合金試樣,得出如下結(jié)論:SLM 成形TC4 合金過程中裂紋主要為冷裂紋,具有典型的穿晶斷裂特征,并指出是由于SLM 成形過程中激光熔化金屬粉末受熱不均,致使成形件組織內(nèi)部產(chǎn)生大的殘余應(yīng)力,另外殘余應(yīng)力的作用下馬氏體組織(抗裂強(qiáng)度低)也會(huì)產(chǎn)生裂紋。Lukas 等[35]研究了工藝參數(shù)對(duì)SLM技術(shù)的β 型TNM-B1 鈦鋁合金裂紋的成因,得出如下結(jié)論:功率和掃描速率較低時(shí),制件容易產(chǎn)生垂直于熔池的裂紋,并認(rèn)為在凝固過程中過快的冷卻速率所產(chǎn)生的殘余應(yīng)力是導(dǎo)致開裂的主要原因。
西北工業(yè)大學(xué)的張鳳英等[36]持相同的看法,也認(rèn)為是工藝參數(shù)選擇不當(dāng),造成SLM 制件內(nèi)部粉末熔合不良,導(dǎo)致制件發(fā)生開裂。劉延輝等[37]研究了激光3D打印TC4 鈦合金根部裂紋產(chǎn)生的原因,微觀組織如圖3 所示,認(rèn)為TC4 鈦合金出現(xiàn)裂紋的根本原因是根部存在組織缺陷、過大的殘余應(yīng)力、性能分布不均以及預(yù)熱溫度不足等共同導(dǎo)致的。劉彥濤等[38]研究功能梯度材料TA15 + Ti2 AlNb 合金激光熔融沉積成形時(shí)發(fā)現(xiàn),激光熔化沉積技術(shù)所制備異種材料的界面為冶金結(jié)合,異種材料結(jié)合界面會(huì)形成過渡區(qū),過渡區(qū)通常是梯度復(fù)合結(jié)構(gòu)的薄弱環(huán)節(jié),容易產(chǎn)生裂紋,此裂紋具有沿界面斷裂的特征,他們認(rèn)為裂紋形成的原因是異種材料界面過渡區(qū)通常會(huì)有對(duì)性能不利的第二相析出,導(dǎo)致材料易沿界面斷裂。
2.4 翹曲變形
翹曲變形是基于粉末床3D打印成形技術(shù)的又一個(gè)難題,經(jīng)常出現(xiàn)在懸伸無(wú)支撐部分,其形成的最根本原因是移動(dòng)的激光點(diǎn)或電子束熱源對(duì)粉末床的不均勻加熱,形成大的溫度梯度,導(dǎo)致材料體系收縮的不一致,主要是熔固收縮和溫致收縮[39, 49]。
其中溫致收縮是指成形件在打印完成后,冷卻至常溫的過程中所產(chǎn)生的收縮,與材料本身的收縮率有關(guān),對(duì)產(chǎn)生翹曲變形作用較?。蝗酃淌湛s是由于粉末經(jīng)激光/電子束熔融后,經(jīng)常產(chǎn)生的一種行為。主要是因?yàn)槌尚芜^程中,粉末經(jīng)加熱后從熔融狀態(tài)轉(zhuǎn)變?yōu)楣虘B(tài),溫差變化較大,故熔固收縮相當(dāng)嚴(yán)重[39, 43]。
翹曲變形對(duì)成形件的尺寸大小、成形精度、形位誤差等的影響很大,甚至?xí)?yán)重影響后續(xù)加工。
國(guó)內(nèi)外針對(duì)鈦合金翹曲變形的研究較少。吳偉輝等[40]對(duì)成形過程中造成翹曲變形的成因進(jìn)行了研究,翹曲變形示意圖如圖4 所示,可以看出激光作用的當(dāng)前層(i) 層,受到高溫的作用處于塑性狀態(tài),在凝固過程中過快的冷卻速率,導(dǎo)致收縮變形;第(i–1) 層溫度略低于第i 層的溫度,此時(shí)塑性較差或處于彈性狀態(tài),在冷卻過程中,其收縮變形小于第(i) 層的變形量,但是在第(i) 層嚴(yán)重翹曲變形的作用下,第(i–1) 層也會(huì)發(fā)生大幅度的向上翹曲變形。同理第(i–2)、(i–3) 層也有相同的影響,只是距離(i) 層越遠(yuǎn),對(duì)應(yīng)層的收縮量越小,當(dāng)距離(i)層到達(dá)一定距離時(shí),對(duì)應(yīng)的層已不發(fā)生收縮變形,翹曲變形終止。齊海波等[41]采用電子束選區(qū)熔化成形TC4 鈦合金成形件,認(rèn)為掃描路徑對(duì)成形件溫度分布的影響,導(dǎo)致熱應(yīng)力分布不均勻是翹曲變形產(chǎn)生的主要原因。楊立寧等[42]通過建立數(shù)值分析模型,研究了在不同掃描路徑和堆積速率下,所對(duì)應(yīng)的熱應(yīng)力場(chǎng)分布和變化行為,以及它們對(duì)制件翹曲變形的影響。李守衛(wèi)等[43]分析了SLS 技術(shù)成形過程中的溫度場(chǎng)與熱應(yīng)力場(chǎng)對(duì)翹曲變形的影響機(jī)理。
3、 鈦合金3D打印成形工藝優(yōu)化
針對(duì)上述各種常見的合金缺陷,國(guó)內(nèi)外學(xué)者運(yùn)用不同的原理,采用不同的工藝優(yōu)化方法對(duì)合金缺陷的抑制進(jìn)行了探究。其中研究較多的方法主要有:對(duì)粉末進(jìn)行預(yù)熱、優(yōu)化工藝參數(shù)或者對(duì)制件進(jìn)行后續(xù)熱處理等,都可以相應(yīng)地改善合金的缺陷,提高合金的組織性能。
3.1 3D打印工藝優(yōu)化
使用不同的成形技術(shù),加工不同的材料,其最優(yōu)的工藝參數(shù)各不相同,合理的設(shè)置工藝參數(shù)(激光功率、掃描速率、掃描間距、掃描策略、層厚、預(yù)熱溫度以及成形氣氛等)能夠明顯減小球化、孔隙、裂紋以及翹曲變形等缺陷。
Fischer 等[44]基于SLS 技術(shù)使用高能量密度的激光(Nd:YAG 激光),對(duì)工業(yè)純Ti 進(jìn)行了激光成形。結(jié)果發(fā)現(xiàn):制件的球化現(xiàn)象明顯得到改善,且成形件的孔隙率也得到提高。Cormier 等[45]認(rèn)為采用預(yù)熱增加粉末黏度,將待熔化粉末加熱到一定的溫度,可有效減少球化現(xiàn)象。張永志等[46]研究發(fā)現(xiàn),通過對(duì)基板進(jìn)行預(yù)熱可降低熔池的凝固速率與成形過程中的溫度梯度,減小SLM 成形合金中的裂紋數(shù)量,但無(wú)法完全消除裂紋。梁曉康等[47]采用SLM 成形技術(shù)制備TC4 鈦合金試樣,研究了工藝參數(shù)對(duì)殘余應(yīng)力的影響。結(jié)果發(fā)現(xiàn):掃描策略對(duì)表面殘余應(yīng)力分布有一定的影響,當(dāng)線能量密度一定時(shí),隨著填充間距的增加,成形層表面殘余應(yīng)力有減小的趨勢(shì)。周旭等[33]研究了近α 鈦合金激光選區(qū)熔化成形開裂機(jī)理及抑制研究,發(fā)現(xiàn)對(duì)工藝進(jìn)行優(yōu)化,可減小組織內(nèi)部的殘余應(yīng)力,從而可有效抑制裂紋的產(chǎn)生;另外還研究了預(yù)熱溫度對(duì)裂紋抑制的影響,發(fā)現(xiàn)裂紋的數(shù)量隨著預(yù)熱溫度的提高逐漸減少,在預(yù)熱溫度提高到350 ℃ 時(shí),裂紋幾乎完全消失。陳靜等[48]研究了TC4 鈦合金的激光快速成形,結(jié)果發(fā)現(xiàn),氧含量嚴(yán)重影響成形件的工藝、表面質(zhì)量和開裂行為,當(dāng)保證氧含量低于0.02%(質(zhì)量分?jǐn)?shù))時(shí),得到的TC4 薄板試樣表面質(zhì)量良好且沒有孔隙、裂紋等缺陷。傅蔡安等[49]研究了掃描路徑對(duì)選擇性激光燒結(jié)工藝成形件的翹曲變形的影響,得出如下結(jié)論:優(yōu)化了掃描路徑不僅大大降低翹曲變形量,而且大大縮短加工時(shí)間提高加工效率。
3.2 后處理工藝優(yōu)化
鈦合金3D打印制件的后處理工序主要有退火、熱等靜壓、固溶時(shí)效、拋光、滲碳等,其中退火的主要目的是減小零件內(nèi)部的殘余應(yīng)力,熱等靜壓則可以減少組織內(nèi)部的孔隙。湯慧萍等[50]在粉末床預(yù)熱的基礎(chǔ)上,結(jié)合隨行熱處理工藝[51],也就是在每完成一層粉末熔化掃描后,再經(jīng)快速掃描實(shí)現(xiàn)緩冷保溫,從而通過塑性及蠕變使應(yīng)力松弛,防止應(yīng)力應(yīng)變累計(jì),達(dá)到減小變形、抑制零件開裂、降低殘余應(yīng)力水平的目的。張霜銀等[52]利用小孔釋放法對(duì)TC4 鈦合金(LENS 技術(shù)成形)沉積態(tài)和熱處理后的殘余應(yīng)力進(jìn)行研究,結(jié)果表明,經(jīng)熱處理后,成形件的殘余應(yīng)力降低顯著,且分布均勻。
Terner 等[53]認(rèn)為金屬粉末在制備過程中所存在的氬氣泡,在隨后的成形過程中會(huì)導(dǎo)致孔隙的產(chǎn)生,它一般呈細(xì)小球狀,再經(jīng)熱等靜壓處理后,孔隙會(huì)再次減小,但不影響材料的力學(xué)性能。
4、鈦合金3D打印技術(shù)的發(fā)展趨勢(shì)
鈦合金3D打印技術(shù)作為一項(xiàng)前沿的制造技術(shù),集設(shè)計(jì)、制造于一體,近年來引起各界廣泛關(guān)注,并在航空航天、國(guó)防軍事、生物醫(yī)學(xué)、汽車高鐵等高精尖領(lǐng)域展示了廣闊的應(yīng)用前景,但是,相較于傳統(tǒng)制造技術(shù)起步較晚,發(fā)展歷史僅30 年左右,與世界先進(jìn)國(guó)家比較還存在很大的差距,比如:鈦合金零件的成形效率低、精度還未能達(dá)到高精水平、設(shè)備和材料的制備成本高,以及仍未實(shí)現(xiàn)大規(guī)模的工業(yè)、商業(yè)應(yīng)用等問題,特別是成形件缺陷的抑制問題。目前我國(guó)對(duì)零件的成形過程中存在的缺陷問題,球化、裂紋、孔隙、翹曲變形等的研究還處于初步階段,仍有大量的研究工作急需進(jìn)行。將來鈦合金3D打印技術(shù)的發(fā)展趨勢(shì)如下:
(1)在材料方面,研制開發(fā)新型的球形鈦合金粉末的生產(chǎn)設(shè)備和制備工藝,提高鈦合金粉末的質(zhì)量(粒度、球形度、流動(dòng)性、夾雜氣體等),進(jìn)而改善制件的組織和力學(xué)性能。此外,通過提高粉末的收得率和粉末的回收再利用來降低成本。
(2)在設(shè)備方面,一方面應(yīng)提高設(shè)備的成形效率、成形精度,以及降低成本等;另外,還要研發(fā)大型的工業(yè)級(jí)打印設(shè)備,逐步實(shí)現(xiàn)大規(guī)模生產(chǎn)和應(yīng)用。
(3)在檢測(cè)方面,伴隨3D打印件向大型化、復(fù)雜化和精密化方向發(fā)展,很多傳統(tǒng)的無(wú)損檢測(cè)方法存在盲區(qū),需要開發(fā)新型的無(wú)損檢測(cè)技術(shù);通過對(duì)組織、缺陷實(shí)時(shí)監(jiān)控的在線檢測(cè)技術(shù)是未來重點(diǎn)的研究方向之一;另外,建立和完善無(wú)損檢測(cè)標(biāo)準(zhǔn),是3D打印技術(shù)廣泛應(yīng)用的依據(jù)。
(4)在工藝方面,進(jìn)一步優(yōu)化3D打印技術(shù)的工藝,抑制成形過程中的缺陷,提高成形件的力學(xué)性能。成形過程中零件內(nèi)應(yīng)力演變規(guī)律、變形開裂行為以及缺陷產(chǎn)生機(jī)理等關(guān)鍵問題,仍然是未來需要重點(diǎn)研究的問題。
參考文獻(xiàn):
[1]喬旭. 鈦合金增材制造技術(shù)的分析和未來趨勢(shì)[J]. 中國(guó)新技術(shù)新產(chǎn)品,2015(23):76.
(QIAO X. Analysis and future trend of titanium alloyaugmentation manufacturing technology[J]. New Technologyand New Products in China,2015(23):76.)
[2]伏欣. 國(guó)內(nèi)增材制造(3D打?。┘夹g(shù)發(fā)展現(xiàn)狀與研究趨勢(shì)[J]. 中國(guó)高新技術(shù)企業(yè),2016(24):27-28.
(FU X. The development status and research trend ofdomestic augmented material manufacturing(3D printing)technology[J]. China Hi-tech Enterprise,2016
(24):27-28.)
[3]譚語(yǔ)夷. 3D打印的技術(shù)現(xiàn)狀與發(fā)展趨勢(shì)[J]. 中國(guó)機(jī)械,2014(11):55.
(TAN Y Y. The technical status and development trendof 3D printing[J]. China Machinery,2014(11):55.)
[4]孫鎮(zhèn)鎮(zhèn). 3D打印材料及其發(fā)展問題與趨勢(shì)[J]. 中國(guó)粉體工業(yè),2016(1):4-6.
(SUN Z Z. 3D printing materials and their developmentproblems and trends[J]. China’s Powder Industry,2016(1):4-6.)
[5]YEONG W Y,CHUA C K,LEONG K F,et al. Rapidprototyping in tissue engineering:challenges and potential[J]. Trends in Biotechnology,2004,22(12):
643-652.
[6] 曾亮華,劉繼常. 金屬 3D打印技術(shù)的發(fā)展分析[J]. 機(jī)械工程師,2016(3):42-44.
[7](ZENG L H,LIU J C. Development of metal 3D printingtechnology analysis[J]. Mechanical Engineer,2016(3):42-44.)
李滌塵,田小永,王永信. 增材制造技術(shù)的發(fā)展[J].電加工與模具,2012(增刊 1):20-22.
(LI D C,TIAN X Y,WANG Y X. Development of additive materials manufacturing technology[J]. ElectricalMachining and Die,2012(Suppl 1):20-22.)
[8]祁斌. 3D打印技術(shù)在船舶領(lǐng)域的應(yīng)用[J]. 中國(guó)船檢,2016(6):94-100.
(QI B. Application of 3D printing technology in shipfield[J]. China Ship Inspection,2016(6):94-100.)
[9]楊強(qiáng),魯中良,黃福享,等. 激光增材制造技術(shù)的研究現(xiàn)狀及發(fā)展趨勢(shì)[J]. 航空制造技術(shù),2016,507(12):26-31.
(YANG Q,LU Z L,HUANG F X,et al. Researchstatus and development trend of laser augmentation manufacturingtechnology[J]. Aviation Manufacturing Technology,2016,507(12):26-31.)
[10]閆占功,林峰,齊海波,等. 直接金屬快速成形制造技術(shù)綜述[J]. 機(jī)械工程學(xué)報(bào),2005,41(11):1-7.
(YAN Z G,LIN F,QI H B,et al. Summary of directmetal rapid prototyping manufacturing technology[J].Journal of Mechanical Engineering,2005,41(11):
1-7.)
[11]錢九紅. 航空航天用新型鈦合金的研究發(fā)展及應(yīng)用[J].稀有金屬,2000,24(3):218-223.
(QIAN J H. Development and application of new titaniumalloys for aerospace[J]. Rare Metals,2000,24(3):218-223.)
[12]SALLICA L E,JARDINI A L,F(xiàn)OGAGNOLO J B.Microstructure and mechanical behavior of porous Ti-6Al-4V parts obtained by selective laser melting[J].
Journal of the Mechanical Behavior of Biomedical Materials,2013,3(26):98-108.
[13]BIRSER E M,MOSKYITIN G V,POLYAKOV AN,et al. Industrial laser cladding: current state and future[J]. Welding Imeraatonal,2011,25(3):234-
243.
[14]KRUTH J P,F(xiàn)ROYEN L,VAEMBERGH J V,et al.Selective laser melting of iron based powder[J]. Journalof Materials Processing Technology,2004,149(1-
3):616-622.
[15]胡孝昀,沈以赴,李子全,等. 金屬粉末激光快速成形的工藝及材料成形性[J]. 材料科學(xué)與工藝,2008,16(3):378-383.
(HU X Y,SHEN Y F,LI Z Q,et al. Processing andmaterial formability of metal powder laser rapid prototyping[J]. Material Science and Technology,2008,
16(3):378-383.)
[16]陳濟(jì)輪,楊潔,于海靜. 國(guó)外高能束增材制造技術(shù)應(yīng)用現(xiàn)狀與最新發(fā)展[J]. 航天制造技術(shù),2014(4):1-4+10.
(CHEN J L,YANG J,YU H J. The abroad applicationand latest development of high-energy beam additivemanufacturing technology[J]. Space Manufacturing
Technology,2014(4):1-4+10.)
[17]劉海濤,趙萬(wàn)華,唐一平. 電子束熔融直接金屬成形工藝的研究[J]. 西安交通大學(xué)學(xué)報(bào),2007,41(11):1126.
(LIU H T,ZHAO W H,TANG Y P. Study on directmetal forming by electron beam melting[J]. Journal ofXi’an Jiaotong University,2007,41(11):1126.)
[18]陳哲源,鎖紅波,李晉煒. 電子束熔絲沉積快速制造成形技術(shù)與組織特征[J]. 航天制造技術(shù),2010(1):40-43.
(CHEN Z Y,SOU H B,LI J W. Rapid prototypingand microstructure characteristics of electron beam fusedeposition[J]. Space Manufacturing Technology,2010
(1):40-43.)
[19]黃秋實(shí),李良琦,高彬彬. 國(guó)外金屬零部件增材制造技術(shù)發(fā)展概述[J]. 國(guó)防制造技術(shù),2012(5):28-31.
(HUANG Q S,LI L Q,GAO B B. Overview of thedevelopment of foreign metal parts manufacturing technology[J]. National Defense Manufacturing Technology,
2012(5):28-31.)
[20]楊平華,高祥熙,梁菁,等. 金屬增材制造技術(shù)發(fā)展動(dòng)向及無(wú)損檢測(cè)研究進(jìn)展[J]. 材料工程,2017,45(9):13-21.
(YANG P H,GAO X X,LIANG J,et al. Developmenttrend of metal additive manufacturing technologyand research progress of nondestructive testing[J]. Materials
Engineering,2017,45(9):13-21.)
[21]趙靜. 機(jī)械零件缺陷的無(wú)損檢測(cè)方法發(fā)展趨勢(shì)[J]. 農(nóng)業(yè)裝備與車輛工程,2005(9):39-40.
(ZHAO J. Development trend of nondestructive testingmethods for defects of mechanical parts[J]. AgriculturalEquipment and Vehicle Engineering,2005(9):39-40.)
[22]肖永順,王鳳娟. 工業(yè)CT 在3D打印領(lǐng)域的新應(yīng)用[C]//全國(guó)射線數(shù)字成像與CT 新技術(shù)研討會(huì). 廈門:[出版者不詳],2014.
(XIAO Y S,WANG F J. New applications of industrialCT in 3D printing[C]//National Symposium on RadiographicDigital Imaging and CT New Technologies. Xiamen,China:[s.n],2014.)
[23]PLESSIS A D,ROUX S G L,ELS J,et al. Applicationof microCT to the non-destructive testing of an additivemanufactured titanium component[J]. Case Studies inNondestructive Testing & Evaluation,2015,4(11):1-7.
[24]王曉,史亦韋,梁菁,等. 激光超聲在線無(wú)損檢測(cè)增材制造零件的方法:CN106018288A[P]. 2016-06-17.
(WANG X,SHI Y W,LIANG J,et al. Methods ofon-line laser ultrasonic nondestructive testing of augmentedmaterials for manufacturing parts:CN106018288A
[P]. 2016-06-17.)
[25]GU D,SHEN Y. Balling phenomena in direct laser sinteringof stainless steel powder: metallurgical mechanismsand control methods[J]. Materials & Design,
2009,30(8):2903-2910.
[26]李瑞迪,魏青松,劉錦輝,等. 選擇性激光熔化成形關(guān)鍵基礎(chǔ)問題的研究進(jìn)展[J]. 航空制造技術(shù),2012,401(5):26-31.
(LI R D,WEI Q S,LIU J H,et al. Research progresson key basic problems of selective laser meltingforming[J]. Aviation Manufacturing Technology,2012,401(5):26-31.)
[27]張曉博. Ti 合金選擇性激光熔化成形關(guān)鍵技術(shù)的研究[D]. 西安:陜西科技大學(xué),2015.
(ZHANG X B. Research on key technologies of selective laser melting of Ti alloy[D]. Xi’an:Shaanxi University of Science and Technology,2015.)
[28]GUSAROV A V,YADROITSEV I,BERTRAND P,et al. Heat transfer modelling and stability analysis of selectivelaser melting[J]. Applied Surface Science,
2007,254(4):975-979.
[29]RAYLEIGH L. On the instability of a cylinder of viscous liquid under capillary force[J]. The London, Edinburgh,and Dublin Philosophical Magazine and Journal of Science,2010,34(207):177-180.
[30]GONG H,RAFI K,GU H,et al. Analysis of defectgeneration in Ti-6Al-4V parts made using powder bed fusion additive manufacturing processes[J]. Additive Manufacturing,
2014(Suppl 1/2/3/4):87-98.
[31]薛蕾,陳靜,張鳳英,等. 飛機(jī)用鈦合金零件的激光快速修復(fù)[J]. 稀有金屬材料與工程,2006,35(11):1817-1821.
(XUE L,CHEN J,ZHANG F Y,et al. Rapid laserrepair of titanium alloy parts for aircraft[J]. Rare MetalMaterials and Engineering,2006,35(11):1817-
1821.)
[32]ZAEH M F,KAHNERT M. The effect of scanningstrategies on electron beam sintering[J]. Production Engineering,2009,3(3):217-224.
[33]周旭,周燕,魏青松,等. 激光選區(qū)熔化近α 鈦合金開裂機(jī)理及抑制研究[J]. 中國(guó)機(jī)械工程,2015,26(20):2816-2820.
(ZHOU X,ZHOU Y,WEI Q S,et al. Study oncracking mechanism and inhibition of near-alpha titaniumalloy by selective laser melting[J]. China MechanicalEngineering,2015,26(20):2816-2820.)
[34]張升,桂睿智,魏青松,等. 選擇性激光熔化成形TC4 鈦合金開裂行為及其機(jī)理研究[J]. 機(jī)械工程學(xué)報(bào),2013,49(23):21-27.
(ZHANG S,GUI R Z,WEI Q S,et al. Study oncracking behavior and mechanism of selective laser meltingforming of TC4 titanium alloy[J]. Journal of Mechanical
Engineering,2013,49(23):21-27.)
[35]LUKAS L,F(xiàn)RANK P S,UTA K,et al. Selective lasermelting of a bete-solidifying TNM-B1 titaniun aluminidealloy[J]. Journal of Materials Processing Technology,2014(214):1852-1860.
[36]張鳳英,陳靜,譚華,等. 鈦合金激光快速成形過程中缺陷形成機(jī)理研究[J]. 稀有金屬材料與工程,2007,36(2):211-215.
(ZHANG F Y,CHEN J,TAN H,et al. Study on thedefect formation mechanism in laser rapid prototyping oftitanium alloys[J]. Rare Metal Materials and Engineering,2007,36(2):211-215.)
[37]劉延輝,瞿偉成,朱小剛,等. 激光3D打印TC4 鈦合金工件根部裂紋成因分析[J]. 理化檢驗(yàn): 物理分冊(cè),2016,52(10):682-685.
(LIU Y H,QU W C,ZHU X G,et al. Cause analysisof cracks in the root of TC4 titanium alloy workpieceduring laser 3D printing[J]. Physical and Chemical Examination:Physical Scroll,2016,52(10):682-685.)
[38]劉彥濤,張永忠,陳以強(qiáng),等. 激光熔化沉積TA15+Ti2AlNb 合金的組織與力學(xué)性能[J]. 航空材料學(xué)報(bào),2017,37(3):61-67.
(LIU Y T,ZHANG Y Z,CHEN Y Q,et al. Microstructure and mechanical properties of laser melting deposited TA15+Ti2AlNb alloys[J]. Journal of Aeronautical
Materials,2017,37(3):61-67.)
[39]帥昌俊. 選擇性激光燒結(jié)翹曲變形抑制研究[D]. 武漢:華中科技大學(xué),2007.
(SHUAI C J. Study on inhibition of warpage of selectivelaser sintering[D]. Wuhan:Huazhong University of Science and Technology,2007.)
[40]吳偉輝,楊永強(qiáng),毛星,等. 激光選區(qū)熔化增材制造金屬零件精度優(yōu)化工藝分析[J]. 鑄造技術(shù),2016(12):2636-2640.
(WU W H,YANG Y Q,MAO X,et al. Process optimizationfor precision manufacturing of metal parts bylaser selective melting and addition[J]. Casting Technology,2016(12):2636-2640.)
[41]齊海波,楊明輝,齊芳娟. 掃描路徑對(duì)電子束選區(qū)熔化TC4 成形件性能影響的數(shù)值模擬[J]. 焊接學(xué)報(bào),2009,30(8):5-8.
(QI H B,YANG M H,QI F J. Numerical simulationof the effect of scanning path on the properties of electricallymelted TC4 parts[J]. Acta Welding,2009,
30(8):5-8.)
[42]楊立寧,單忠德,戎文娟,等. 金屬件熔融堆積3D打印過程熱應(yīng)力場(chǎng)數(shù)值模擬[J]. 鑄造技術(shù),2016(4):753-758.
(YANG L N,SHAN Z D,RONG W J,et al. Numericalsimulation of thermal stress field in 3D printing processof metal melt deposition[J]. Foundry Technology,
2016(4):753-758.)
[43]李守衛(wèi),沈以赴,顧冬冬,等. 選擇性激光燒結(jié)金屬件翹曲與開裂問題的研究進(jìn)展[J]. 激光雜志,2005,26(5):4-6.
(LI S W,SHEN Y F,GU D D,et al. Progress in researchon warpage and cracking of metal parts in selectivelaser sintering[J]. Laser Journal,2005,26(5):
4-6.)
[44]FISHCHER P,ROMANO V,WEBER H P,et al. Sinteringof commercially pure titanium powder with a Nd:YAG laser source[J]. Acta Materialia,2003,51
(6):1651-1662.
[45]CORMIER D,HARRYSSON O,WEST H. Characterizationof H13 steel produced via electron beammelting[J]. Rapid Prototyping Journal,2004,10(1):35-41.
[46]張永志,侯慧鵬,彭霜,等. 激光選區(qū)熔化HastelloyX 合金的顯微組織與拉伸性能的各向異性[J]. 航空材料學(xué)報(bào),2018,38(6):50-56.
(ZHANG Y Z,HOU H P,PENG S,et al. Anisotropyof microstructure and mechanical properties ofHastelloy X alloy produced by selective laser melting[J].
Journal of Aeronautical Materials,2018,38(6):50-56.)
[47]梁曉康,陳濟(jì)輪,嚴(yán)振宇,等. 激光選區(qū)熔化成形TC4鈦合金表面粘粉及殘余應(yīng)力研究[J]. 電加工與模具,2016(5):52-55.
(LIANG X K,CHEN J L,YAN Z Y,et al. Study onsurface adhesive powder and residual stress of TC4 titaniumalloy formed by laser selective melting[J]. Electromachiningand Mold,2016(5):52-55.)
[48]陳靜,楊海歐,湯慧萍,等. 成形氣氛中氧含量對(duì)TC4鈦合金激光快速成形工藝的影響[J]. 中國(guó)材料進(jìn)展,2004,23(3):23-26.
(CHEN J,YANG H O,TANG H P,et al. Effect of oxygen content in forming atmosphere on laser rapid prototypingprocess of TC4 titanium alloy[J]. Progress of
Materials in China,2004,23(3):23-26.)
[49]傅蔡安,陳佩胡. 選擇性激光燒結(jié)的翹曲變形與掃描方式的研究[J]. 鑄造,2008,57(12):1237-1240.
(FU C A,CHEN P H. Study on warpage deformationand scanning mode of selective laser sintering[J]. Casting,2008,57(12):1237-1240.)
[50]湯慧萍,王建,逯圣路,等. 電子束選區(qū)熔化成形技術(shù)研究進(jìn)展[J]. 中國(guó)材料進(jìn)展,2015,34(3):225-235.
(TANG H P,WANG J,LU S L,et al. Research progressof electron beam selective melting technology[J].Progress in Materials in China,2015,34(3):225-235.)
[51]TANG H P,YANG G Y,JIA W P,et al. Additive manufacturing of a high niobium-containing titanium aluminide alloy by selective electron beam melting[J]. Ma-
terials Science & Engineering:A,2015,636:103-107.
[52]張霜銀,林鑫,陳靜,等. 熱處理對(duì)激光立體成形TC4殘余應(yīng)力的影響[J]. 稀有金屬材料與工程,2009,38(5):774-778.
(ZHANG S Y,LIN X,CHEN J,et al. Effect of heattreatment on residual stress of laser stereoformingTC4[J]. Rare Metal Materials and Engineering,2009,38(5):774-778.)
[53]TERNER M,BIAMINO S,EPICOCO P,et al. Electronbeam melting of high niobium containing TiAl alloy:feasibility investigation[J]. Steel Research International,2012,83(10):943-949.
相關(guān)鏈接